增材制造 W-Ni-Fe 系高比重合金的研究進(jìn)展
發(fā)布時(shí)間:
2024-12-27
高比重鎢合金是一種以鎢為主體,加入少量Ni、Fe、Cu、Co、Mn等元素組成的合金,其鎢質(zhì)量分?jǐn)?shù)一般為85%~98%,密度可達(dá)16.5~19.0g/cm3,因此又常常被稱(chēng)為高比重合金、重合金或高密度鎢合金[1]。高比重鎢合金主要分為W-Ni-Fe和W-Ni-Cu兩大體系,其組織主要由W相和Ni-Fe/Cu粘接相兩相組成。相較于W-Ni-Cu系合金,W-Ni-Fe系合金有著更為優(yōu)異的物理力學(xué)性能,主要表現(xiàn)在抗拉強(qiáng)度高、延性好、具有良好的機(jī)加工特性等[2],因此在國(guó)防工業(yè)和國(guó)民經(jīng)濟(jì)各領(lǐng)域發(fā)揮著巨大的作用,如穿甲彈彈芯材料、煙霧彈、脫殼彈等武器材料[3];陀螺儀外緣轉(zhuǎn)子[4]、直升機(jī)轉(zhuǎn)子葉片等航空航天材料[5];放射性屏蔽材料、砧塊材料等核工業(yè)材料[6]。
W-Ni-Fe系合金零部件的制造通常采用粉末冶金液相燒結(jié)(liquidphasesintering,LPS)的方式。一般是將各元素粉末機(jī)械混合,經(jīng)過(guò)模壓或冷等靜壓成形,然后采用LPS達(dá)到全致密形成毛坯件,最終采用機(jī)械加工的手段去除余量,得到最終零部件。在粉末冶金過(guò)程中,模壓和冷等靜壓需首先根據(jù)最終零部件的形狀與尺寸設(shè)計(jì)與制備相應(yīng)的模具,而模具制作周期長(zhǎng),費(fèi)用昂貴;且考慮到LPS易變形坍塌的特點(diǎn),粉末冶金的方式一般只適用于具有簡(jiǎn)單形狀或留有較大機(jī)加余量毛坯體的制備。同時(shí),采用粉末冶金的方式制備鎢合金零件一般需要模具,而模具的生產(chǎn)周期較長(zhǎng),不適用于定制化、小批量產(chǎn)品的制備[7]。
增材制造技術(shù)由于具有近凈成形,加工數(shù)字化、智能化、自動(dòng)化,原材料利用率高,無(wú)需模具,組織細(xì)小均勻等優(yōu)點(diǎn),被廣泛應(yīng)用于小批量、定制化、高復(fù)雜度金屬零部件的制造[8]。常見(jiàn)的金屬增材制造技術(shù)主要包括選區(qū)激光熔化技術(shù)(selectivelasermelting,SLM)、激光熔化沉積技術(shù)(lasermeltingdeposition,LMD)和選區(qū)電子束熔化技術(shù)(selectiveelectronbeammelting,SEBM)。
近年來(lái),國(guó)內(nèi)外學(xué)者針對(duì)高比重W-Ni-Fe系合金、高比重W-Ni-Cu系合金[9-15]以及純W[16-18]的SLM、LMD和SEBM增材制造進(jìn)行了廣泛研究。除SLM、LMD和SEBM技術(shù)外,粘接劑噴射打印技術(shù)(binderjetprinting,BJP)也被應(yīng)用于高比重W-Ni-Fe系合金制備。
本文將對(duì)國(guó)內(nèi)外利用SLM、LMD、SEBM、BJP4項(xiàng)技術(shù)進(jìn)行的高比重W-Ni-Fe系合金增材制造的研究進(jìn)展進(jìn)行綜述,并對(duì)研究面臨的主要問(wèn)題、研究趨勢(shì)進(jìn)行分析和展望。
1 選區(qū)激光熔化W-Ni-Fe系合金
SLM技術(shù)(技術(shù)原理如圖1所示)采用分層制造的思想,以激光束作為熱源,成形時(shí)先在基板上鋪平一定厚度的粉末,然后激光按規(guī)劃軌跡輻射粉末,使輻射范圍內(nèi)粉末經(jīng)歷熔化和凝固的過(guò)程,單層掃描完成后,再在該層之上鋪平一層粉末,重復(fù)上述熔化、凝固、鋪粉步驟直至成型完成。SLM技術(shù)采用微熔池逐層堆積方法,具有近凈成形、無(wú)需模具等特點(diǎn),十分適用于小尺寸、復(fù)雜形狀、力學(xué)性能優(yōu)異的零件成形。目前報(bào)道的增材制造W-Ni-Fe合金多用SLM技術(shù)制備。
Zhang和李瑞迪等人[19-22]采用不同的激光功率和掃描速度進(jìn)行了90W-7Ni-3Fe的SLM研究,建立了90W-7Ni-3Fe合金的加工圖,將成形工藝分為了4個(gè)加工窗口(見(jiàn)圖2):(i)適度熔化區(qū)域,(ii)球化區(qū)域,(iii)微熔化區(qū)域和(iv)不熔化區(qū)域。在適度熔化區(qū)域(高激光功率和低掃描速度),由于輸入的激光能量較高,可以生成相對(duì)致密、表面無(wú)明顯裂紋的試件,是目前SLM技術(shù)優(yōu)選的工藝參數(shù)區(qū)域;在球化區(qū)域(高的激光功率和高掃描速度),輸入的激光能量不足以完全熔化W粉,產(chǎn)生球化現(xiàn)象,導(dǎo)致試樣致密度不良;在微熔化區(qū)域(中等激光功率和低掃描速度),輸入的激光能量不足以完全熔化Ni、Fe粉,導(dǎo)致部分Ni、Fe粉殘留,試樣缺陷增多;在不熔化區(qū)域(低激光功率和低掃描速度),Ni、Fe粉末能熔化,無(wú)法與W粉結(jié)合。D.Q.Zhang等人[19]認(rèn)為隨著輸入的激光能量的增加,W-Ni-Fe的SLM成形機(jī)制會(huì)從LPS機(jī)制(完全熔化的Ni-Fe粉末與未完全熔化W粉)向粉末熔化—凝固機(jī)制(W粉完全熔化)轉(zhuǎn)變,W顆粒組織形貌經(jīng)歷了顆粒狀向枝晶狀轉(zhuǎn)變的過(guò)程(見(jiàn)圖3)?;趦?yōu)化的工藝,R.D.Li等人采用SLM技術(shù)實(shí)現(xiàn)了90W-7Ni-3Fe合金的葉片構(gòu)件成形[22]。
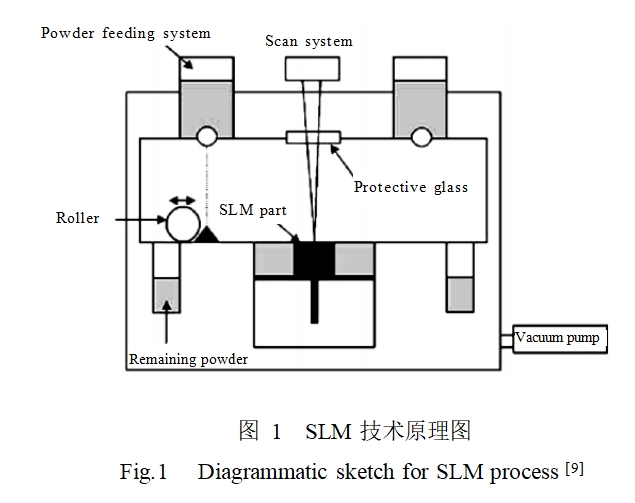
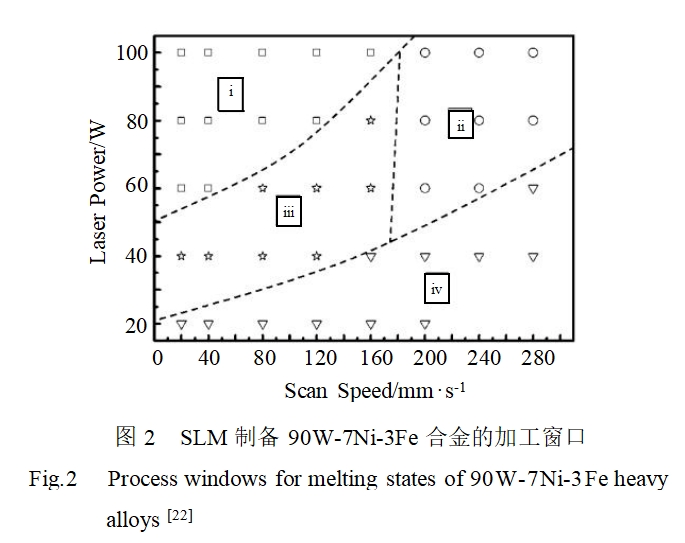
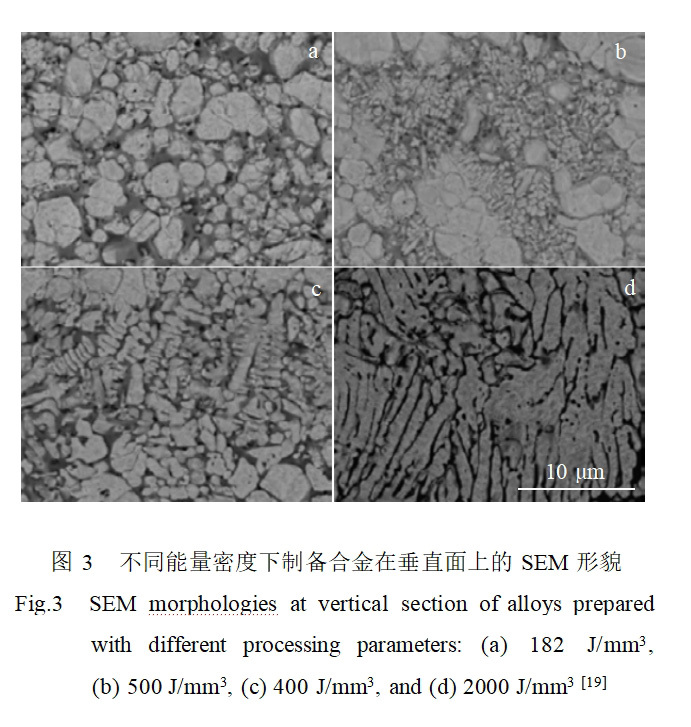
Wang[23]等人研究了激光掃描跡線(xiàn)寬度、激光功率和掃描速度等激光參數(shù)對(duì)SLM制備的90W-7Ni-3Fe合金的致密度影響。研究表明,90W-7Ni-3Fe合金的致密度同時(shí)主要受W顆粒的重排以及W的溶解-析出過(guò)程控制,同時(shí)激光功率和掃描速度對(duì)其致密度影響顯著,通過(guò)工藝參數(shù)優(yōu)化,其制備的90W-7Ni-3Fe合金最大致密度可達(dá)94.5%。
Alja?Ivekovi?[24]等人研究了激光能量密度、預(yù)先加熱、后熱處理對(duì)SLM制備90W-7Ni-3Fe合金組織與性能的影響,也發(fā)現(xiàn)隨著激光能量密度的增加,90W-7Ni-3Fe合金的成形機(jī)制從LPS向部分熔化到完全熔化轉(zhuǎn)變,其加工窗口如圖4所示,成形鎢合金的組織分別如圖5所示。當(dāng)能量密度過(guò)低時(shí),成形鎢合金的密度較低,且Ni-Fe粘結(jié)相含量比初始粉末組成更高。在較高的能量密度下,特別是在400℃預(yù)熱下,F(xiàn)e和Ni的氣化使成形合金富W且極易開(kāi)裂。在中等能量密度下,即W顆粒部分熔化時(shí),成形的W-Ni-Fe合金具有高強(qiáng)度(抗拉強(qiáng)度為871±30MPa)低塑性(延伸率<1%)的性能。對(duì)該成形樣品進(jìn)行了類(lèi)似重新LPS的高溫退火處理(1500℃,保溫30~60min),合金的顯微組織和性能(抗拉強(qiáng)度為850±21MPa,延伸率為(10.2±1.0)%)可與傳統(tǒng)LPS方法制備的零件相當(dāng)。
Li等人[25]研究了激光能量密度在185到778J/mm3范圍內(nèi)90W-7Ni-3Fe合金的SLM成形。發(fā)現(xiàn)在該能量范圍內(nèi),90W-7Ni-3Fe合金的成形組織類(lèi)似于LPS,呈現(xiàn)W顆粒或W枝晶鑲嵌于粘接相的組織;通過(guò)工藝參數(shù)優(yōu)化,實(shí)現(xiàn)了高致密度(≥99%)、高強(qiáng)度(抗拉強(qiáng)度1121MPa)和低塑性(延伸率<1%)90W-7Ni-3Fe合金的成形。
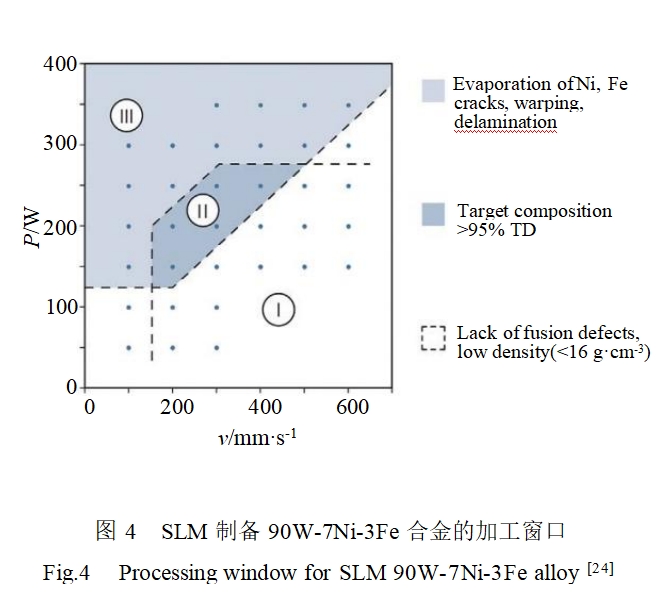
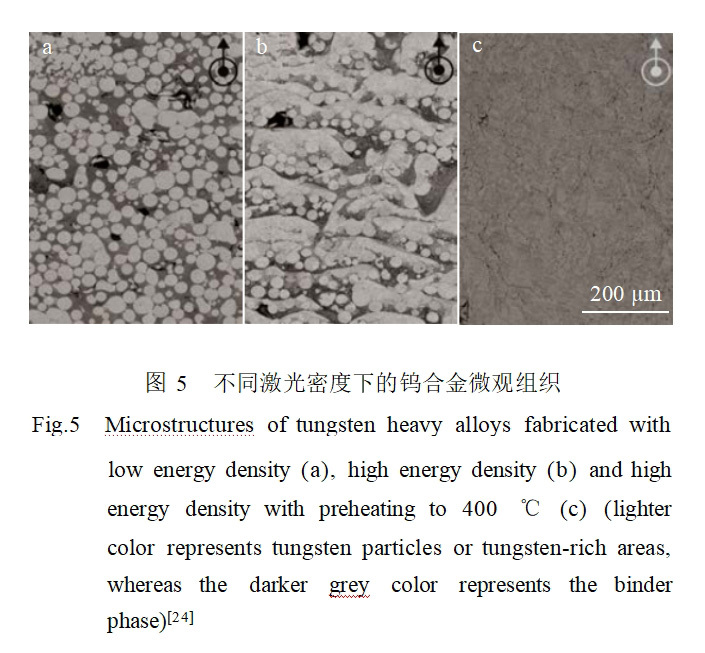
Chen等人[26]在W-Ni-Fe合金中添加Co,研究了70W、80W和90W合金的SLM成形,發(fā)現(xiàn)隨著激光功率的增大,材料的密度增加,實(shí)現(xiàn)了致密度達(dá)96%的70W制備。當(dāng)W含量較低時(shí),成形合金中存在Fe7W6金屬間化合物,當(dāng)W質(zhì)量分?jǐn)?shù)增加到90%時(shí),成形合金中出現(xiàn)裂紋。成形合金中W顆粒形態(tài)為多角形和枝晶形,隨著W含量的減小,W枝晶所占比例增加。在激光功率為350W,掃描速度為400mm/s時(shí),制備的70W-18Ni-6Fe-6Co最大抗拉強(qiáng)度為1198MPa,延伸率在7%~9.5%之間。
整體來(lái)說(shuō),采用SLM技術(shù),已實(shí)現(xiàn)了含W質(zhì)量分?jǐn)?shù)達(dá)90%、致密度大于99%的W-Ni-Fe系合金的制備。在中等能量密度下制備W-Ni-Fe系合金時(shí)具有LPS的特點(diǎn),其組織也與常規(guī)LPS方式制備的W-Ni-Fe系合金類(lèi)似,合金表現(xiàn)為成形性好,不開(kāi)裂,且SLM制備的90W合金可具有比常規(guī)LPS樣品更高的抗拉強(qiáng)度,但其塑性一般較差(<1%)。通過(guò)后高溫?zé)崽幚?,或是降低合金中的W含量,可以獲得較好的強(qiáng)塑性綜合性能。現(xiàn)有SLM技術(shù)制備W-Ni-Fe合金多采用元素混合粉,而在鋪粉過(guò)程中難以保證各元素粉能均勻鋪展于成形平臺(tái)上,有可能導(dǎo)致成形區(qū)和未熔化區(qū)粉末的成分不均勻,使得未熔化粉體與原始粉末相比成分發(fā)生變化,給粉末的回收再利用帶來(lái)了一定的挑戰(zhàn)[27]。
2 激光熔化沉積W-Ni-Fe系合金
LMD技術(shù)(技術(shù)原理如圖6所示)起源于激光表面熔覆技術(shù)[28],同時(shí)結(jié)合快速原型制造技術(shù),利用高能量密度激光將同步送達(dá)的金屬粉按規(guī)劃路徑進(jìn)行熔覆,單層熔覆完成之后,將激光頭和送粉頭抬升一定高度,重復(fù)層內(nèi)熔覆過(guò)程,最終實(shí)現(xiàn)工件逐層熔化、快速凝固堆積成型。由于在該技術(shù)發(fā)展初期,各國(guó)研究機(jī)構(gòu)獨(dú)立開(kāi)展了相關(guān)研究,導(dǎo)致這項(xiàng)技術(shù)擁有眾多別稱(chēng),如:激光近凈成形(laserengineerednetshaping,LENS)、激光金屬沉積(lasermetaldeposition,LMD)、激光立體成形(lasersolidforming,LSF)、受控激光制造(directedlaserfabrication,DLF)、金屬直接沉積(directmetaldeposition,DMD)、激光固化(laserconsolidation,LC)、激光金屬成型(lasermetalforming,LMF)、光控制造(directlightfabrication,DLF)、激光直接制造(laserdirectmanufacturing,LDM)、激光自由成型制造(laserfree-formfabrication,LFFF)[29]等。相較于SLM技術(shù),LMD技術(shù)的成形效率較高,更適用于大尺寸零部件的制備。
鐘敏霖等人[30,31]率先研究了45W-55Ni、60W-40Ni、和90W-10Ni3種鎢合金體系的LMD成形,發(fā)現(xiàn)前兩者均有良好的成形性,而90W-10Ni體系成形性較差,表現(xiàn)為隨著沉積高度的增加,薄壁成形件的厚度不斷減小,導(dǎo)致僅能成形截面為三角形的薄壁。
90W合金的成形性較差可能是因?yàn)椴捎肅O2激光器,而金屬對(duì)該波段激光吸收率較低導(dǎo)致。通過(guò)工藝優(yōu)化,鐘敏霖等人成功實(shí)現(xiàn)了直徑30mm,高度307mm,壁厚3mm的60W-40Ni太空望遠(yuǎn)鏡準(zhǔn)直器縮小比例樣件的制備。

王攀等人[32,33]在大氣環(huán)境下采用W原子分?jǐn)?shù)為60%~90%的W-Ni-Fe混合粉末進(jìn)行了LMD成形研究,并進(jìn)行了組織觀(guān)察與拉伸力學(xué)性能測(cè)試,發(fā)現(xiàn)成形鎢合金具有與常規(guī)粉末冶金樣件類(lèi)似的W顆粒鑲嵌于粘接相基底中的組織,當(dāng)W原子分?jǐn)?shù)為60%時(shí),制備的合金具有最佳的力學(xué)性能,其抗拉強(qiáng)度可達(dá)718MPa。隨著W含量的增加,制備合金的力學(xué)強(qiáng)度反而不斷降低,推測(cè)是由于成形是在大氣環(huán)境中,導(dǎo)致合金氧化嚴(yán)重出現(xiàn)了明顯的孔洞、裂紋等缺陷。
Wang等人[34,35]研究了W質(zhì)量分?jǐn)?shù)為80%~85%的W-Ni、W-Ni-Fe、W-Ni-Co合金的LMD成形,發(fā)現(xiàn)成形合金中W顆粒具有不規(guī)則形狀和枝晶形狀2種形態(tài),而枝晶W主要存在于層間(如圖7a所示),且隨著激光功率的增加,枝晶狀W顆粒所占比例增加;同時(shí)發(fā)現(xiàn)在粘接相中存在著細(xì)小的柱狀晶,且柱狀晶的生長(zhǎng)方向在熔池底部時(shí)平行于沉積方向,在熔池頂部時(shí)平行于掃描方向(如圖7b所示);隨著Fe、Co含量的增加,試樣的強(qiáng)塑性增加,且Co比Fe有著更好的提升力學(xué)性能的效果,如圖8所示。
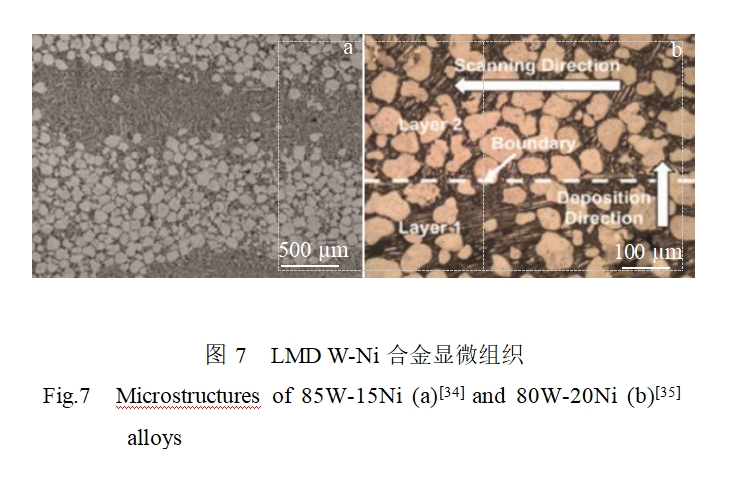
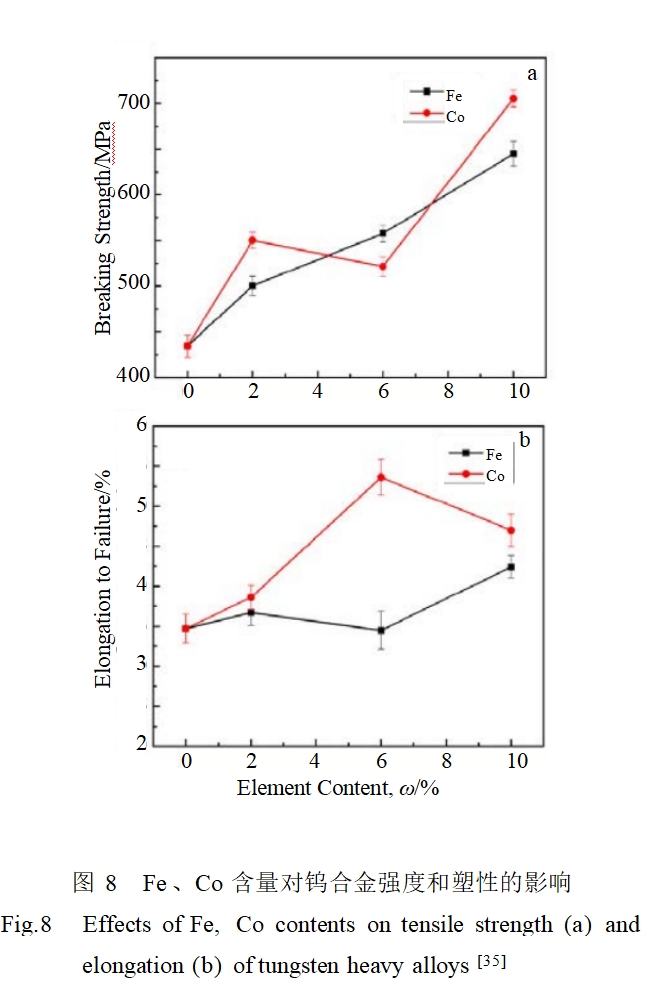
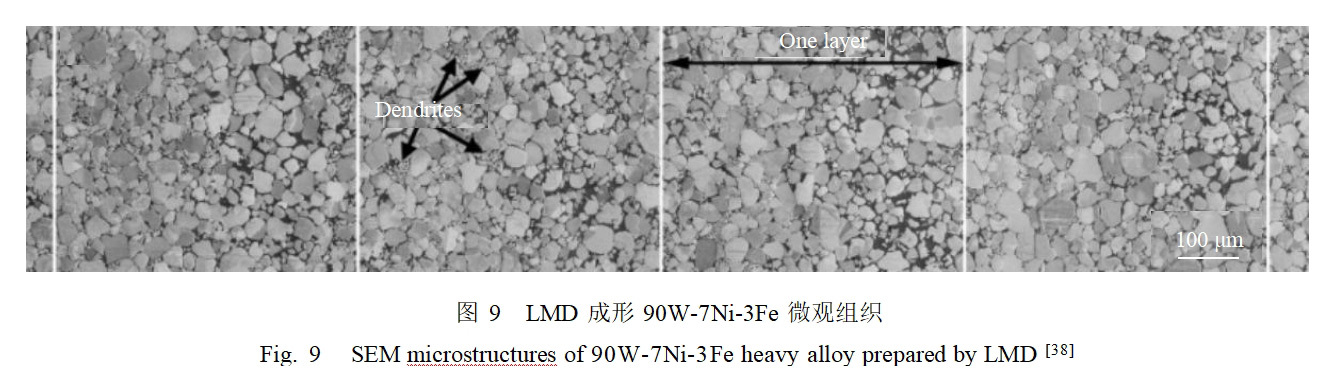
Li等人[36,37]研究了80W-20Fe合金的LMD成形,發(fā)現(xiàn)成形組織主要由不規(guī)則W顆粒、W枝晶、Fe7W6殼體/顆粒、Fe基粘接相組成,其中不規(guī)則W顆粒主要為未溶W粉,而W枝晶為凝固過(guò)程中從液相中析出長(zhǎng)大的W晶體,W枝晶的含量隨著輸入能量密度的增加而增加,而Fe7W6相形成于非平衡冷卻過(guò)程中的包晶反應(yīng);細(xì)小的W枝晶以及Fe7W6相使得合金硬度增加,整體呈現(xiàn)脆性。在后續(xù)研究中,Li等人[38]研究了90W-7Ni-3Fe合金的LMD成形,發(fā)現(xiàn)成形組織中未生成金屬間化合物,同時(shí)隨著輸入能量密度的增加,合金中的大尺寸未熔合孔洞缺陷減少,樣件致密度增加,然而在高輸入能量密度下樣件中依然存在著微米級(jí)的氣孔,當(dāng)輸入激光能量密度達(dá)到74J/mm3時(shí),可實(shí)現(xiàn)致密度>99%的90W-7Ni-3Fe合金的成形;同時(shí)發(fā)現(xiàn)由于W顆粒在微溶池中由于重力影響發(fā)生沉降,使得W顆粒沿著沉積方向呈現(xiàn)周期性疏密分布,如圖9所示;參照傳統(tǒng)粉末冶金LPS過(guò)程,提出了W-Ni-Fe合金在LMD過(guò)程中的類(lèi)似LPS機(jī)制的組織演變過(guò)程,如圖10所示。在LMD過(guò)程中,由于原始W粉部分溶解,使得成形組織中的W顆粒比原始W粉末要更圓潤(rùn)且尺寸更小。Y.P.Wang等人[39]對(duì)LMD和LPS制備的90W-7Ni-3Fe合金的組織與性能進(jìn)行了對(duì)比研究,發(fā)現(xiàn)LMD合金的W-W顆粒連接度更小,粘接相中具有更高的W含量,且在W顆粒和粘接相內(nèi)部具有更高的位錯(cuò)密度,這些特征使得LMD合金具有更高的強(qiáng)度(抗拉強(qiáng)度可達(dá)到1037MPa),如圖11所示。
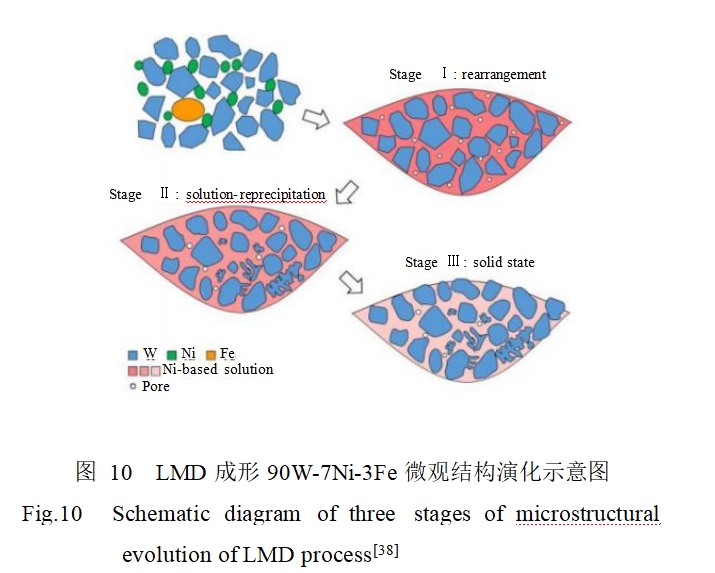
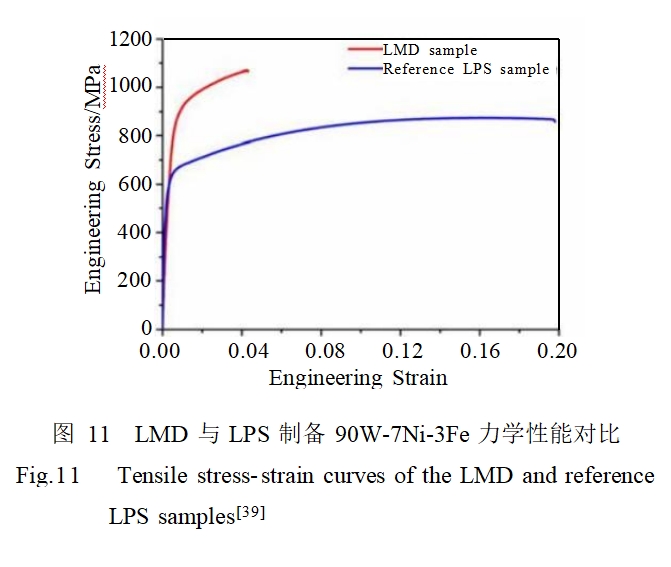
Zhou等人[40]采用LMD技術(shù)避免了傳統(tǒng)粉末冶金制備低W含量合金時(shí)的變形與坍塌問(wèn)題,實(shí)現(xiàn)了低W含量的75W-17.5Ni-7.5Fe合金和50W-35Ni-15Fe合金的成形,同時(shí)發(fā)現(xiàn)LMD方法制備的75W-17.5Ni-7.5Fe和50W-35Ni-15Fe合金具有細(xì)小均勻分布的W顆粒組織,且抗拉強(qiáng)度可分別達(dá)到1120和1316MPa,該強(qiáng)度已超過(guò)傳統(tǒng)粉末冶金95W合金的抗拉強(qiáng)度,如圖12所示。
目前,采用LMD技術(shù)已實(shí)現(xiàn)了W質(zhì)量分?jǐn)?shù)達(dá)90%,致密度大于99%的W-Ni-Fe系合金的制備,制備的合金具有與常規(guī)粉末冶金LPS方式制備的W-Ni-Fe系合金類(lèi)似的組織,即由W相鑲嵌于粘接相中。LMD制備的W-Ni-Fe合金的抗拉強(qiáng)度可遠(yuǎn)超過(guò)傳統(tǒng)粉末冶金W-Ni-Fe合金,達(dá)到1300MPa水平,但塑性一般在6%以下。在工藝層面上,如何調(diào)配更為合適的工藝參數(shù)以解決成型件內(nèi)部的孔洞冶金缺陷也將是LMD技術(shù)發(fā)展的重要方向。
3 選區(qū)電子束熔化高比重鎢合金
與SLM相類(lèi)似,EBSM(技術(shù)原理如圖13所示)的制造過(guò)程也是先在基板上平鋪一層粉末,然后電子束按照預(yù)設(shè)軌跡熔化粉末,待粉末凝固后重復(fù)鋪粉、熔化、凝固步驟直至零件成型。該方法也適用于小尺寸、復(fù)雜形狀零件的成形,但目前關(guān)于W-Ni-Fe合金的研究報(bào)道還較為少見(jiàn)。
楊廣宇等人[42]研究了線(xiàn)能量密度對(duì)EBSM制備的90W-7Ni-3Fe合金致密化的影響,發(fā)現(xiàn)在低的線(xiàn)能量密度下合金的致密化過(guò)程主要為W相粘結(jié),隨著線(xiàn)能量密度的增加,W顆粒重排能力提升,且在粘接相中發(fā)生溶解和析出,而能量密度進(jìn)一步增加則會(huì)造成W顆粒的熔化以及Ni、Fe元素的揮發(fā)。線(xiàn)能量密度的增加使得W在粘接相中含量增加,由此產(chǎn)生固溶強(qiáng)化,使得粘接相顯微硬度提升,如圖14所示。
相比于激光成形技術(shù),EBSM技術(shù)由于采用磁偏轉(zhuǎn)線(xiàn)圈進(jìn)行電子束的移動(dòng)控制,其移動(dòng)無(wú)機(jī)械慣性,可以在成形的過(guò)程中快速掃描粉末層實(shí)現(xiàn)粉床預(yù)熱,從而減小成形過(guò)程中的溫度梯度,減小熱應(yīng)力集中,降低變形開(kāi)裂的風(fēng)險(xiǎn)[43]。同時(shí)相比于激光,金屬材料對(duì)電子束的吸收率更高,在成形過(guò)程中不會(huì)像激光成形一樣,形成熔池后溫度急劇升高從而導(dǎo)致材料氣化[44],可更有效地避免低熔點(diǎn)Ni、Fe元素的氣化,因此在W-Ni-Fe合金的增材制造上可具有獨(dú)特的優(yōu)勢(shì)。但其和SLM技術(shù)一樣存在粉末回收利用的難題。
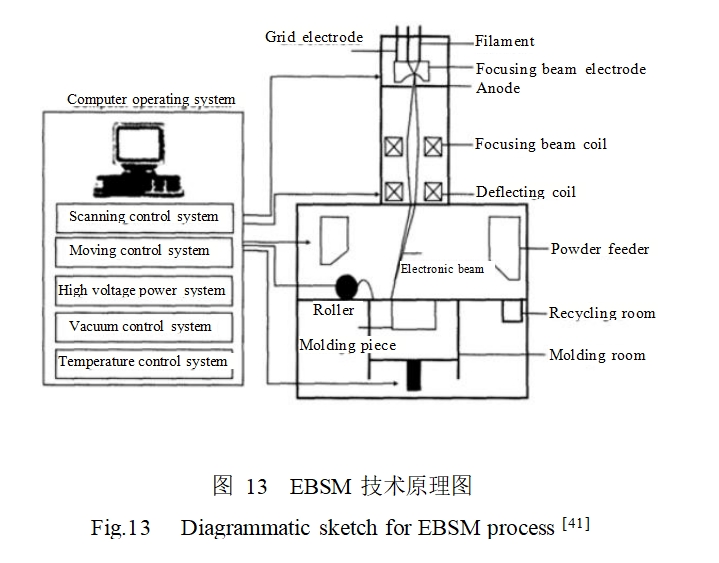
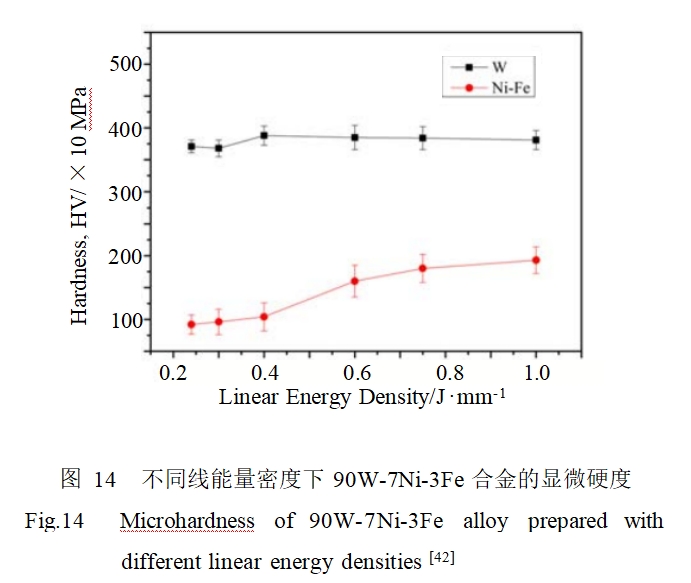
4 粘接劑噴射打印
BJP技術(shù)(技術(shù)原理如圖15所示)的工作原理是將粉末鋪散于成形平臺(tái)上,通過(guò)噴射聚合物粘合劑將粉末按設(shè)定形狀選擇性粘合在一起,如此多層重復(fù)鋪粉與噴粘合劑形成零件毛壞,再將毛坯加熱以固化膠粘劑,固化后將多余的散粉去除,再進(jìn)行脫蠟和燒結(jié)后處理形成最終零件[45,46]。
Stawovya等人[47]采用特有專(zhuān)有技術(shù)制備的預(yù)合金粉(如圖16所示),利用BJP技術(shù)制備了成形件毛坯,再將毛坯在870℃脫蠟后在1365~1385℃下燒結(jié)2h,最終成功實(shí)現(xiàn)了密度為17.24g/cm3,抗拉強(qiáng)度為770MPa,延伸率為8.6%的91W-Ni-Fe合金制備。
與基于激光和電子束的增材制造技術(shù)相比,BJP技術(shù)不需要由激光和電子束作用產(chǎn)生高溫熔池,因此,其制造成本較低,且可避免低熔點(diǎn)Ni、Fe元素的氣化問(wèn)題,但其最終零部件的制備還需要結(jié)合傳統(tǒng)的脫脂和燒結(jié)過(guò)程,流程較長(zhǎng),且粘接劑的殘留有可能對(duì)最終零部件的性能產(chǎn)生不利影響。
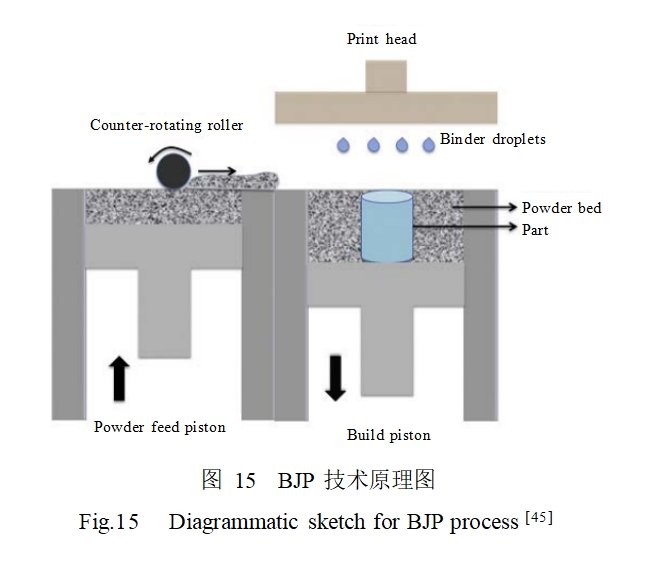
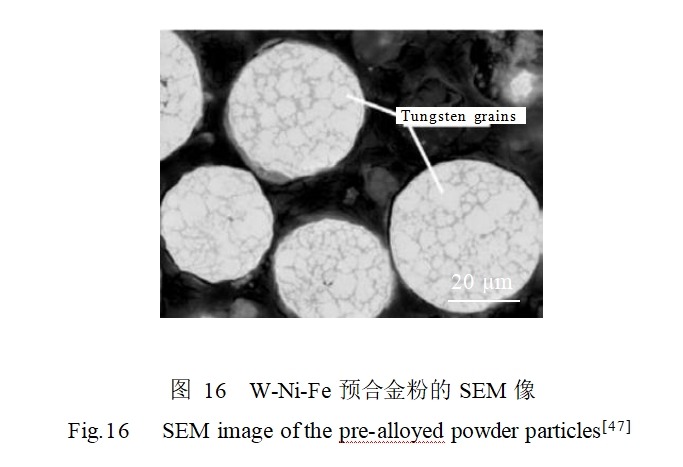
5 W-Ni-Fe系合金增材制造技術(shù)對(duì)比分析
對(duì)4種W-Ni-Fe系合金增材制造技術(shù)從W含量、組織特征、力學(xué)性能、優(yōu)缺點(diǎn)進(jìn)行對(duì)比分析,結(jié)果如表1所示。
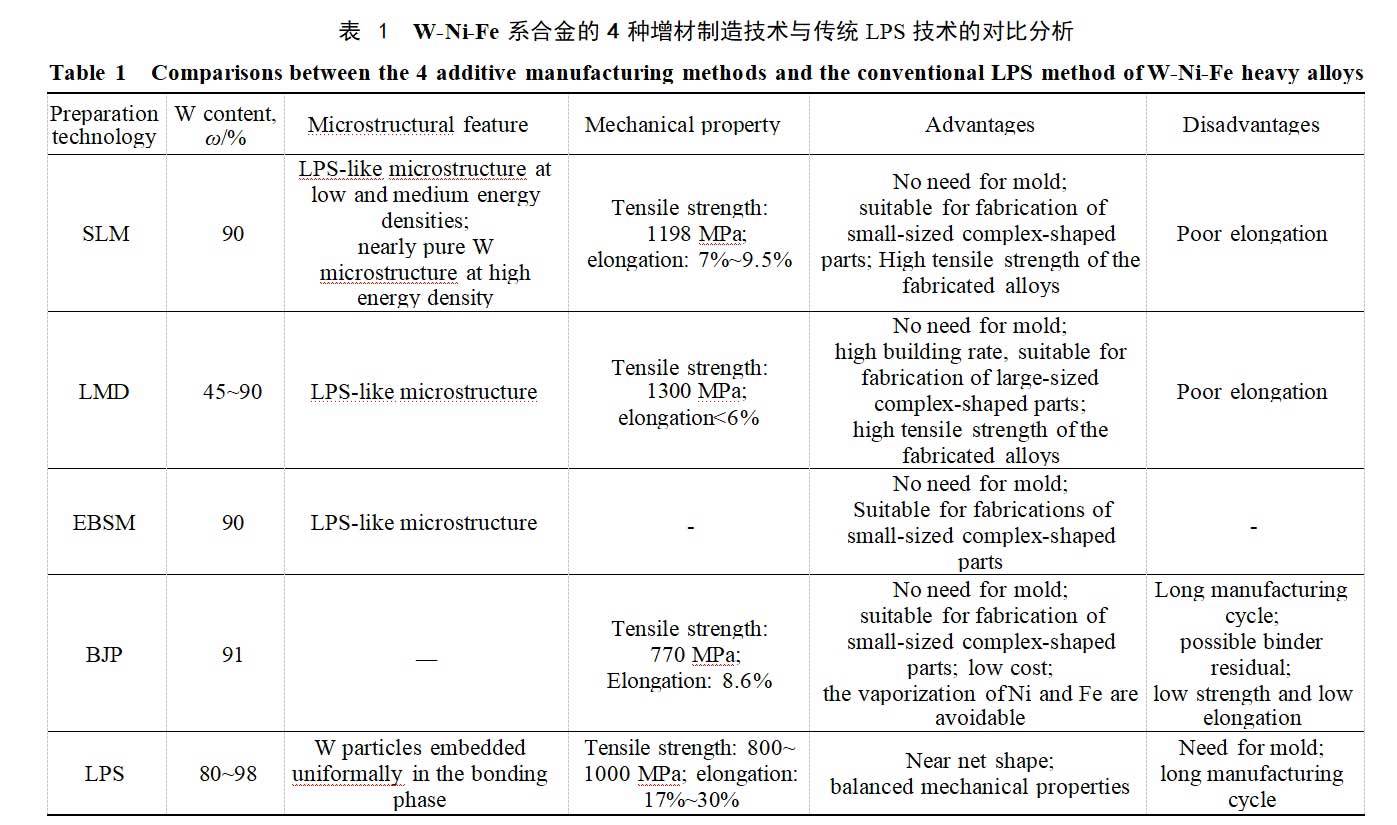
經(jīng)過(guò)10來(lái)年的發(fā)展,增材制造W-Ni-Fe系合金的研發(fā)取得了較大的進(jìn)展。通過(guò)工藝優(yōu)化,采用SLM、LMD、EBSM和BJP技術(shù)都已實(shí)現(xiàn)W質(zhì)量分?jǐn)?shù)達(dá)90%樣品的致密成形,但還未進(jìn)行更高W質(zhì)量分?jǐn)?shù)(91%以上)合金的增材制造研發(fā)。采用SLM和LMD技術(shù)制備的合金力學(xué)強(qiáng)度可遠(yuǎn)高于傳統(tǒng)LPS制備的樣品,但在塑性方面離傳統(tǒng)LPS制備的樣品還有較大差距。
原材料粉末是制約W-Ni-Fe系合金增材制造的關(guān)鍵因素之一。由于W-Ni-Fe系合金是由W相和Ni-Fe-W粘接相兩相組成,W相以顆粒形態(tài)均勻分散于粘接相中,其組織類(lèi)似于一種復(fù)合材料。而W熔點(diǎn)高、體積占比高(通常大于80%[48],且W相和粘接相的熔點(diǎn)差異巨大(純W的熔點(diǎn)甚至超過(guò)了粘接相的沸點(diǎn)[49]),使得采用霧化方法(包括氣霧化和等離子體旋轉(zhuǎn)電極離心霧化)制備預(yù)合金粉末的難度較大。在氣霧化的加熱保溫過(guò)程中由于高熔點(diǎn)W的體積占比高,難以完全溶解于液態(tài)粘接相中而以固相存在,使得熔體無(wú)法穩(wěn)定均勻流出坩堝或保溫包,因此難以氣霧化制備W-Ni-Fe系預(yù)合金粉。而采用等離子體旋轉(zhuǎn)電極離心霧化方式制備W-Ni-Fe預(yù)合金粉時(shí),由于W相和粘接相的熔點(diǎn)差異巨大,W-Ni-Fe合金棒中的粘接相在高溫作用下會(huì)先軟化或熔化,從而易導(dǎo)致大塊的合金塊在離心力的作用下脫離合金棒,形成大塊爐渣,使得球形預(yù)合金粉末的收得率低下?,F(xiàn)有W-Ni-Fe系合金的增材制造多采用元素混合粉,而給W-Ni-Fe系合金的增材制造帶來(lái)了較多如粉末回收、組織均勻性控制等挑戰(zhàn)。僅文獻(xiàn)[38]報(bào)道在W-Ni-Fe系合金的BJP成形中采用了預(yù)合金粉,但并未透露該預(yù)合金粉的制備方法,以及收得率、球形度、成分均勻化控制的相關(guān)信息。
雜質(zhì)含量(尤其是氧含量)也是影響W-Ni-Fe系合金性能的關(guān)鍵因素之一[50]。傳統(tǒng)LPS過(guò)程一般采用氫氣燒結(jié)工藝,可以有效地降低合金樣品中的氧含量,因此可不嚴(yán)格控制原材料粉末的氧含量。但在增材制造工藝過(guò)程中,還難以采用氫氣氣氛,因此對(duì)原材料粉末中的氧含量要求更高,對(duì)原材料粉末的制備提出了更高的純凈度要求。
6 總結(jié)與展望
采用LMD、SLM、EBSM和BJP技術(shù),均已實(shí)現(xiàn)了W質(zhì)量分?jǐn)?shù)達(dá)90%的W-Ni-Fe系合金的成形,其中,采用SLM和LMD技術(shù)制備的90W合金致密度可大于99%。當(dāng)采用合適的能量密度、增材制造成形件的組織與傳統(tǒng)LPS組織類(lèi)似時(shí),SLM和LMD制備的W-Ni-Fe合金的抗拉強(qiáng)度均可遠(yuǎn)超過(guò)傳統(tǒng)LPSW-Ni-Fe合金,其中LMD制備的W-Ni-Fe合金抗拉強(qiáng)度已可達(dá)到1300MPa水平,但SLM和LMD制備的W-Ni-Fe合金塑性都較差,一般在9.5%以下。
整體來(lái)說(shuō),國(guó)內(nèi)外對(duì)于W-Ni-Fe系合金的增材制造研究仍處于發(fā)展階段,當(dāng)前的研究主要是基于激光或電子束增材制造技術(shù)開(kāi)展。當(dāng)采用激光或電子束作為熱源時(shí),由于其快速凝固的特點(diǎn),增材制造的W-Ni-Fe合金可具有特殊的組織,如枝晶形W晶粒、粘接相中固溶W含量更高、W-W顆粒連接度更低、晶粒內(nèi)部位錯(cuò)密度更高等,這些特征使得增材制造的W-Ni-Fe合金較傳統(tǒng)LPS技術(shù)制備的W-Ni-Fe合金可具有更高的力學(xué)強(qiáng)度。但增材制造制備的W-Ni-Fe合金易產(chǎn)生內(nèi)部微觀(guān)組織分布不均勻,存在孔洞、裂紋等缺陷而導(dǎo)致其延性較差,制約了產(chǎn)品的應(yīng)用。
W-Ni-Fe系合金的增材制造研究目前還主要是處于科研探索角度,重點(diǎn)針對(duì)90W-7Ni-3Fe這個(gè)合金進(jìn)行了詳細(xì)的工藝窗口開(kāi)發(fā)、組織與性能研究,但還未能解決其塑性差的問(wèn)題。未來(lái)還需要對(duì)成形工藝、組織與性能關(guān)系進(jìn)行深入探討,從原材料粉末、合金成分、成形工藝、后熱處理等方面進(jìn)行組織性能調(diào)控研究,明晰其強(qiáng)韌化機(jī)制,以提升增材制造W-Ni-Fe合金的性能。同時(shí)需對(duì)其他W含量,尤其是更高W含量的合金的增材制造進(jìn)行探索研究。原材料粉末也是制約其發(fā)展的一個(gè)重要因素,如何制備高純凈度的預(yù)合金粉也將是未來(lái)需要重點(diǎn)關(guān)注的問(wèn)題之一。
參考文獻(xiàn):(c)1994-2022 china Academic Journal Electronic pubolishing House. Al rights reserved. http://www.cnki.net
星塵科技采用射頻等離子體球化技術(shù)制備的球形鎢鎳鐵合金粉,具備高球形度、低氧含量和優(yōu)異的流動(dòng)性,適用于增材制造(3D打印)、注射成型和高性能零部件的精密制造。其優(yōu)勢(shì)在于提高成品致密度與力學(xué)性能,廣泛應(yīng)用于航空航天、軍工制造和高端裝備領(lǐng)域。
有球形稀有難熔金屬粉末的需求,可隨時(shí)聯(lián)系我們的專(zhuān)業(yè)人員。鄭經(jīng)理 13318326187。
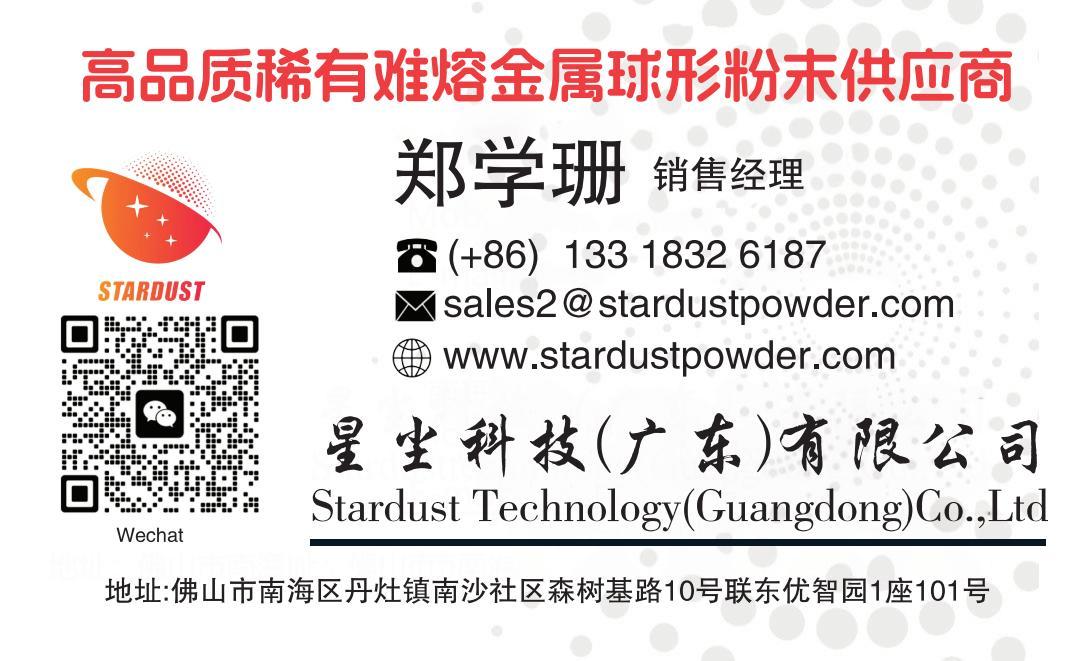
相關(guān)新聞